Batik in Times of Covid
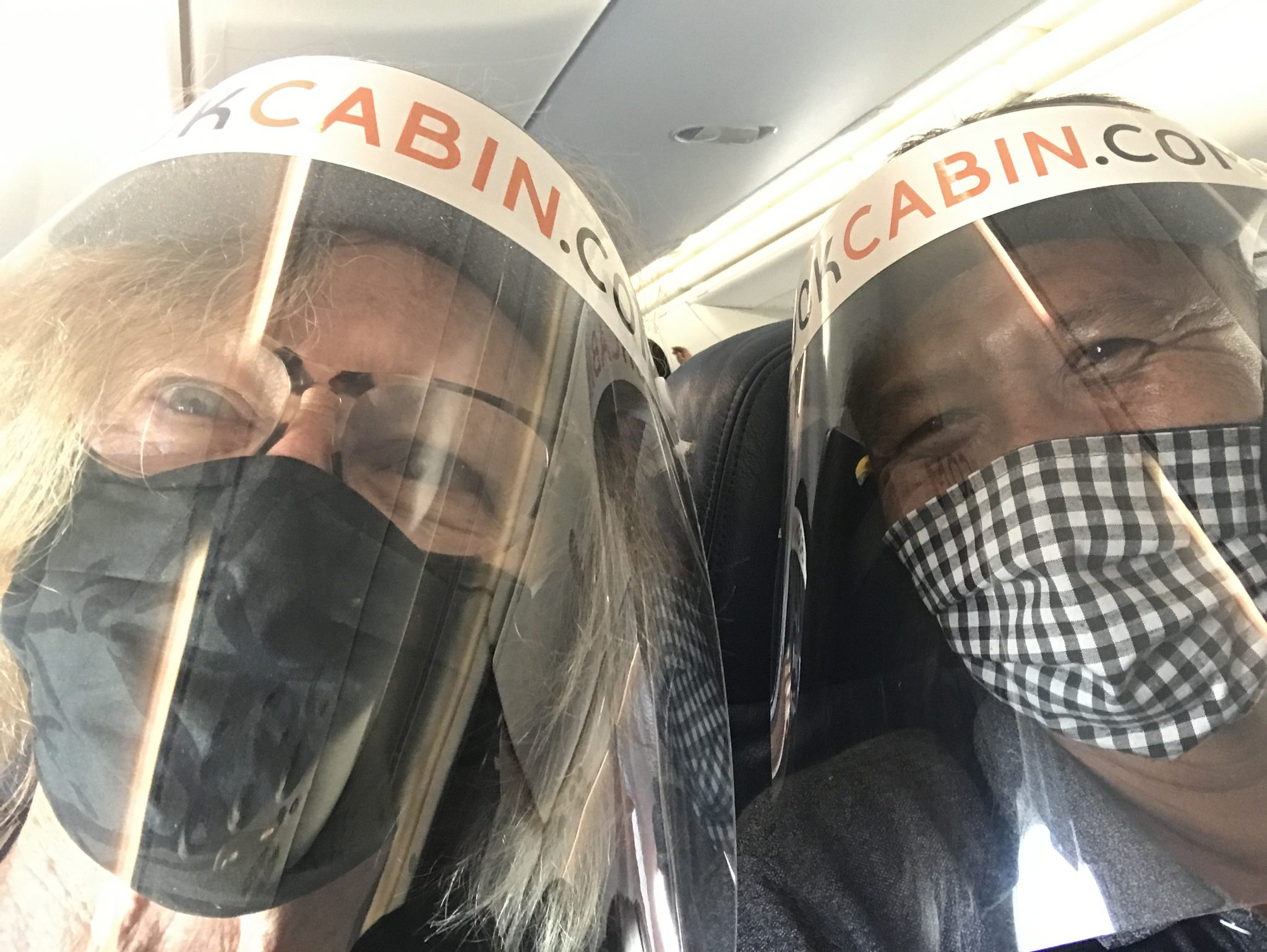
Pung And Jean Don Face Shields On Their Trip To Solo To Meet The Lou Zeldis Artisans
In Indonesia, very little is accomplished unless it is done face-to-face, which is clearly hard to achieve during this Coronavirus Pandemic. Our negotiations with the artisans in Java to take over Lou Zeldis’s twenty-year batik textile production with them were at a stalemate for this very reason. Contracts had been drawn up based on our obligations to Lou’s estate, but the main producer in Java insisted that we meet before he sign. “I want you to feel you can trust me and I want to feel that I can trust you”. These relationships are then always sealed over shared meals. After trying every possible way to convince him that phone calls were enough and that we could meet when things were safer, Pung and I decided we needed to step out of our isolation and fly to Java.
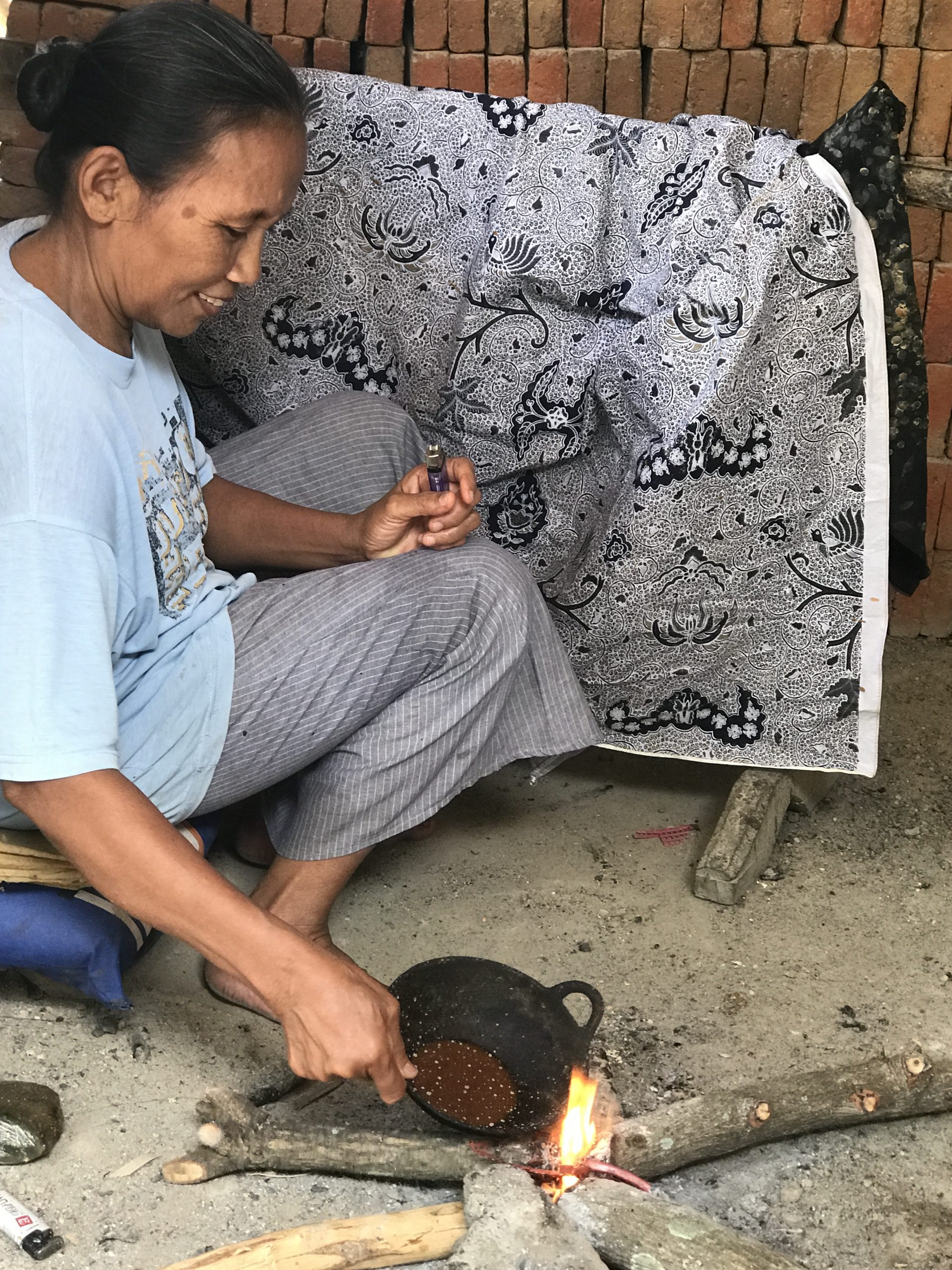
A Batik Artist Burns Plastic To Melt Her Wax As She Cannot Afford Kerosene
Besides being able to meet Lou’s artisans, we found our short trip to Solo and Yogyakarta invaluable in that it gave us an essential snapshot of how hard-hit communities are in these times of Covid. The economic impact due to loss of business, as in most places across the world, is incredible. I thought that Bali was having a rough time, but big cities like Yogyakarta and Solo appeared to be experiencing a much harder situation. What we learned about the economics of producing batik textiles provided us with an insight into what is likely happening for small businesses throughout Indonesia.
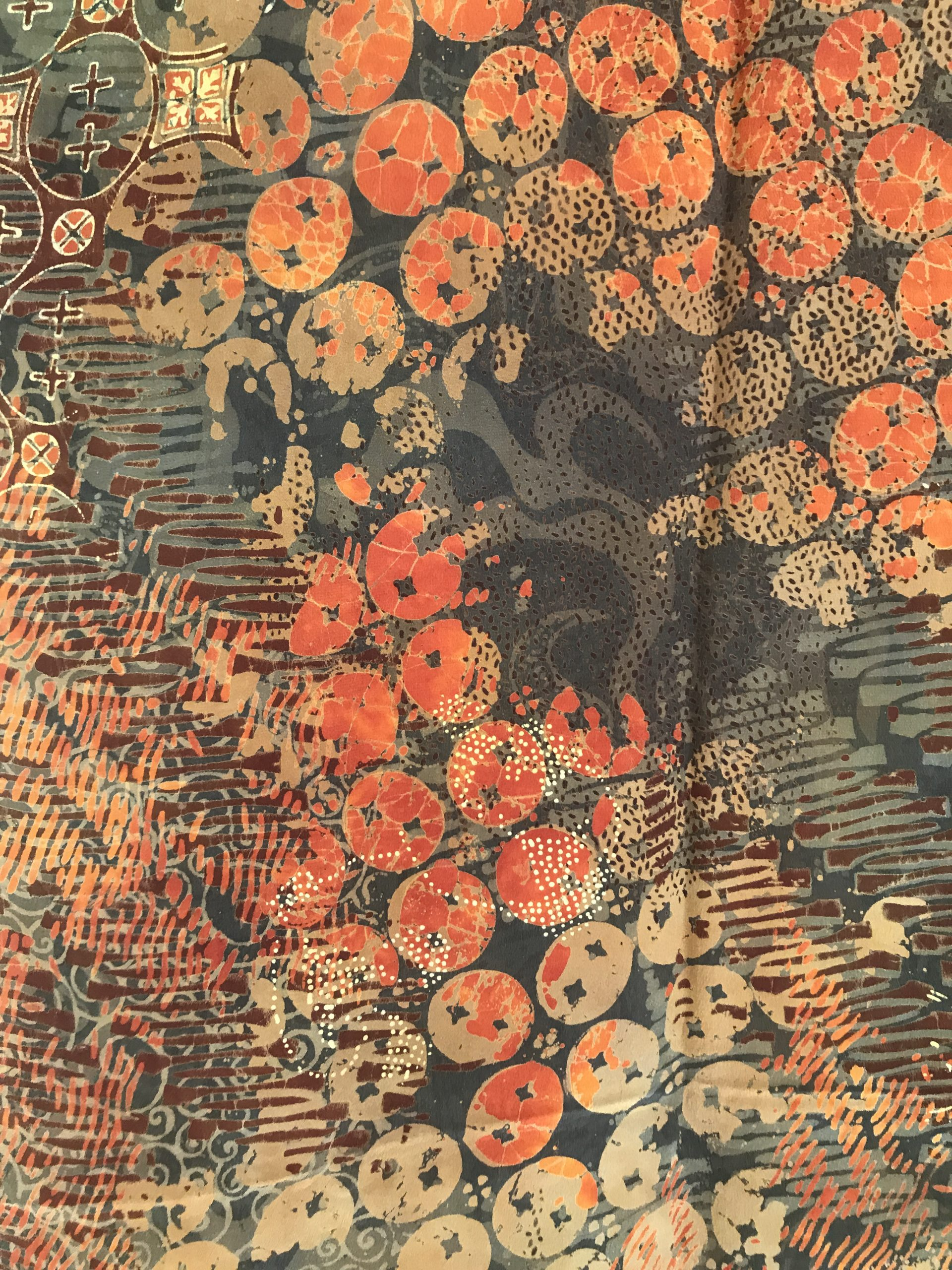
Combining Handmade Stamp Patterns With An Overlay Of Hand Drawn Patterns Using Canting
Traditional batik involves the application to cloth of waxes that resist dyes thereby revealing patterns once the wax is removed. Wax can be hand drawn onto cloth using a canting tool or it can be applied with stamps made from copper sheet. At the Brahma Tirta Sari studio in Yogjakarta they use both processes to make their exquisite silk scarves.
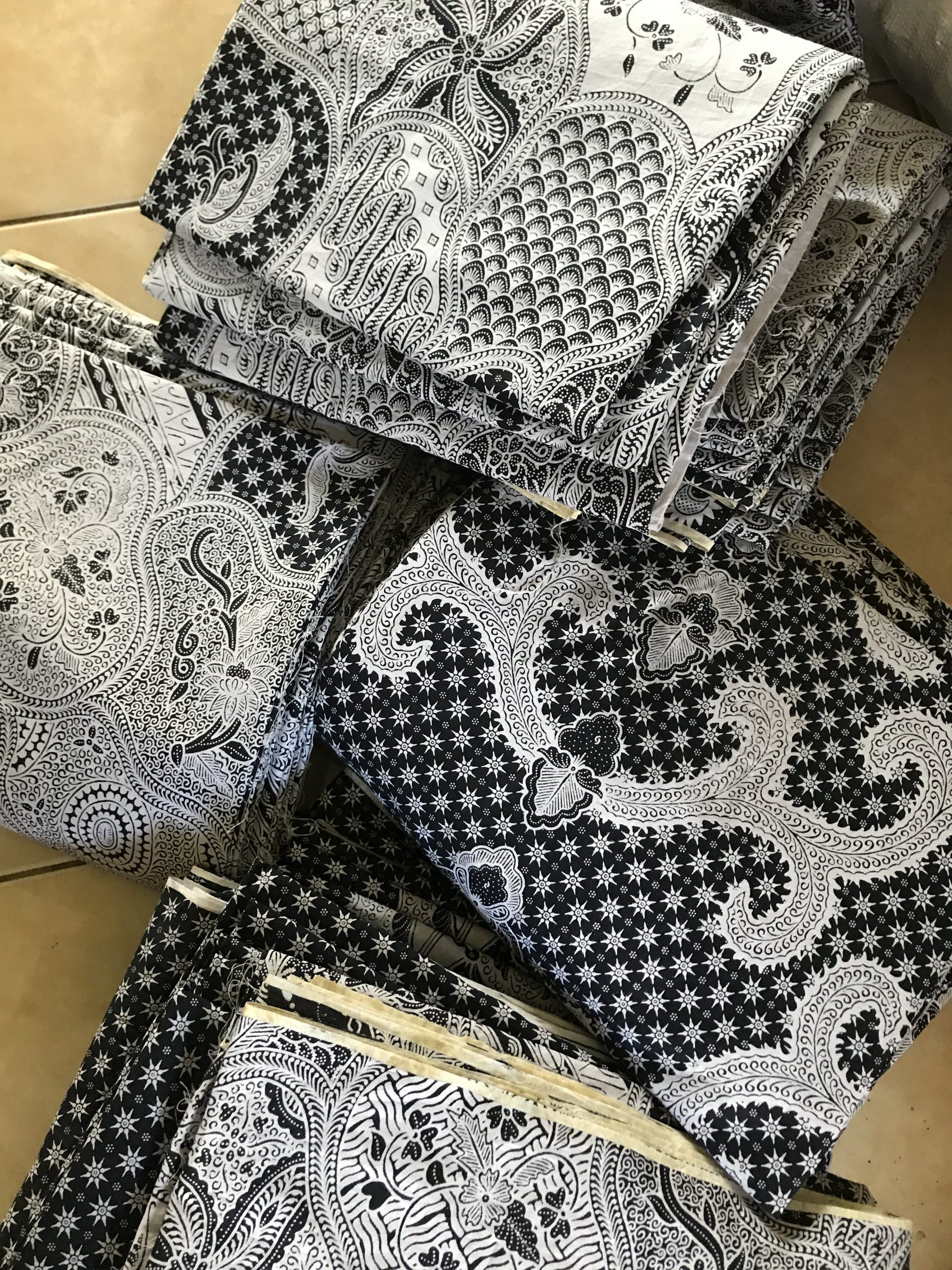
Printed Black And White Cloth Cut To 2.5 Meters
A new market for cheap natural dyed textiles in Java has emerged with this pandemic. The cheapest way to meet this demand for natural dyed “traditional batik” is to buy cloth that has been printed with a black pattern in factories and precut into the traditional length of 2.5 meters, and then over-dye it with the traditional soga brown dye.
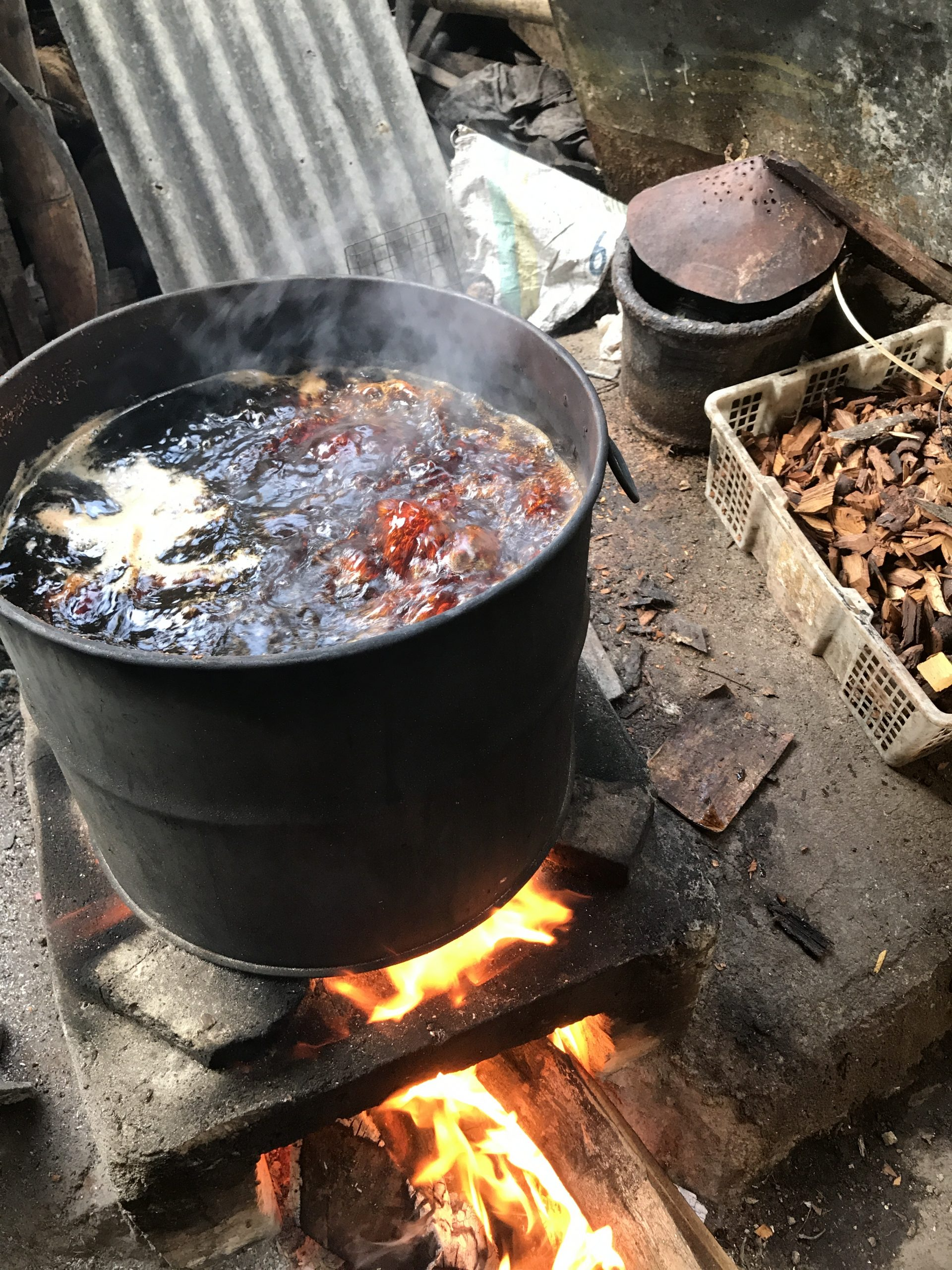
Boiling Barks And Woods For Soga Dye Work
In fully natural dyed production, the foundational pattern is dyed with indigo. After re-waxing the cloth, over-dyeing with a brown dye called soga turns the indigo areas black and makes other non-waxed areas brown. Soga is a deep brown colour that utilizes heart wood of Maclura cochinchinensis (Javanese: tegeran), bark from Peltophorum pterocarpum (Javanese: jambal), and bark of Ceriops tegal (Javanese: tingi). None these are sustainably harvested, especially the very slow growing Maclura cochinchinensis.
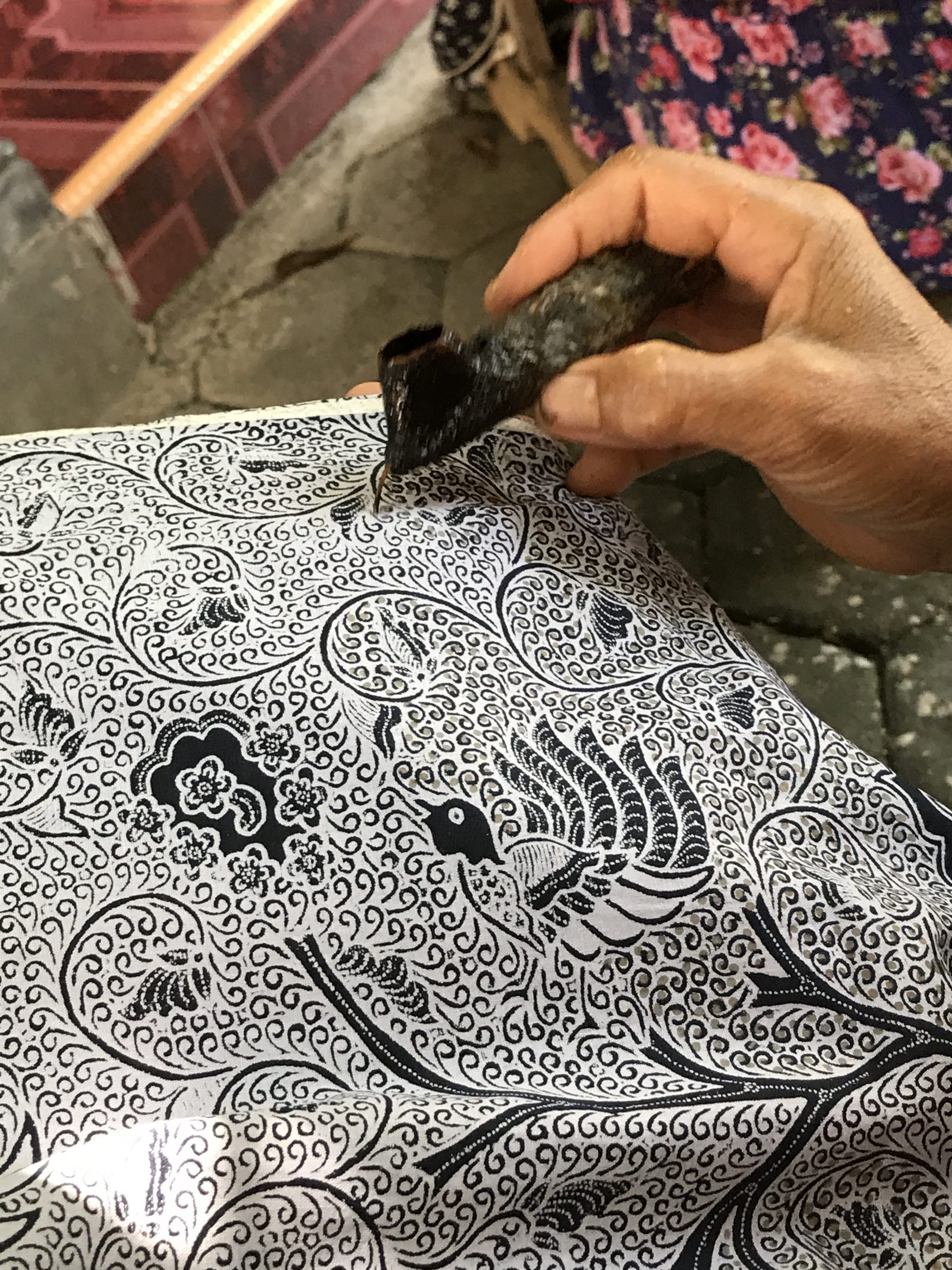
Waxing A Background Using A Canting Tool On The Printed Cloth
Hard working soga dyers would not have made “natural dyed cloth” by over-dyeing printed meterage in the past, but they are now faced with no income from the higher-end market that once supported them and need fast cash to feed families. One length of printed cloth costs IDR 100,000. The batik artist receives IDR 75,000 for her work, and having been dyed with soga fifty-five times, the dyer sells a finished piece for between IDR 200,000 and IDR 250,000 wholesale. A net income of up to IDR 75,000 (USD 5, AUD 7) per piece barely covers expenses and gives no real profit.
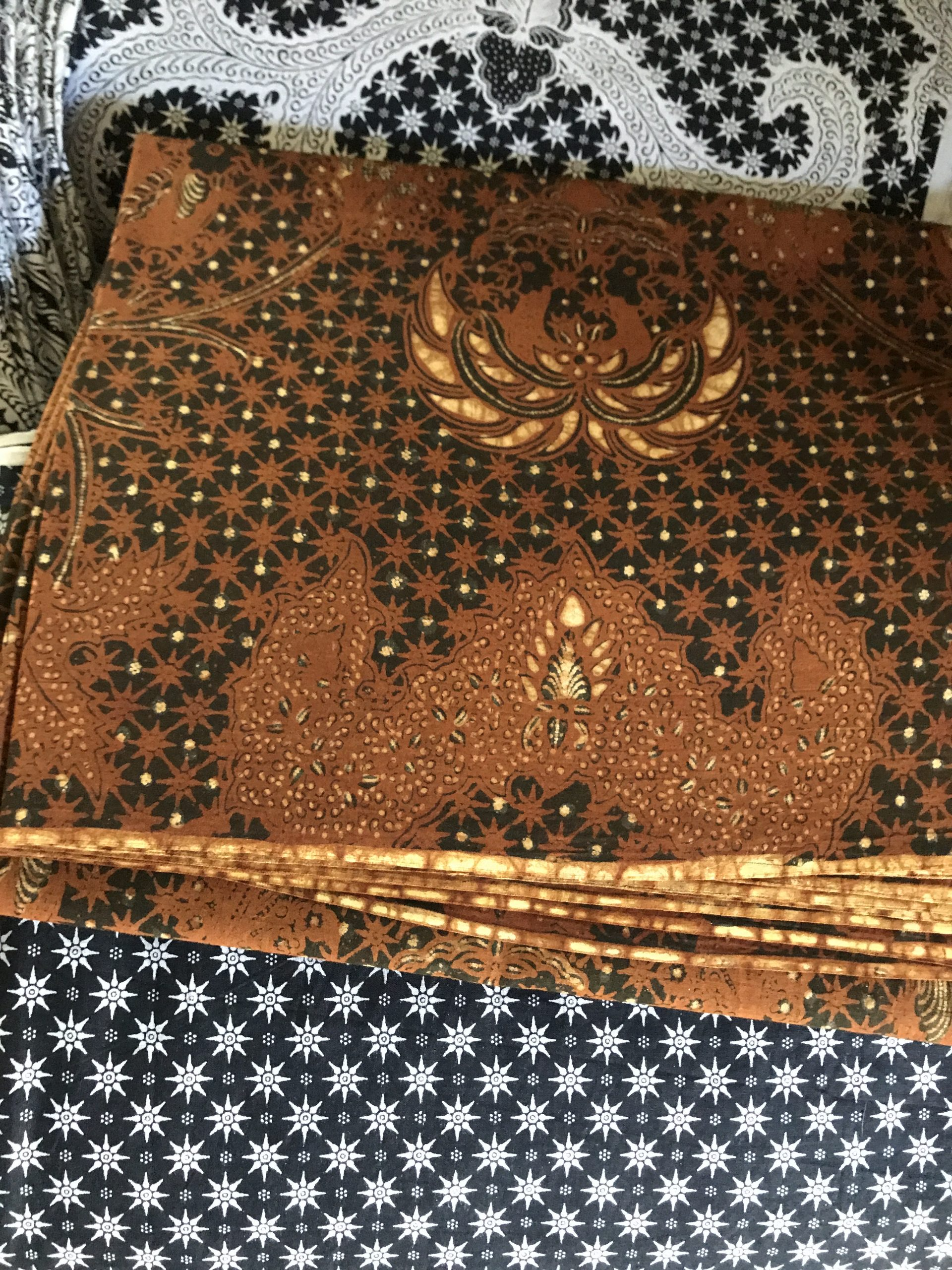
The Stars Are Dyed Brown And The Print Black Background Is Overdyed In Brown Which Makes It A Richer Color
Here we can see a cloth that has been dyed with soga on top of the kind of print it was made from. If you look at the star pattern in the undyed and dyed cloth you can see that the only part that was waxed to resist color is the tiny 6-dot pattern between the stars. The stars are dyed brown and the print black background is overdyed in brown to make it a richer color.
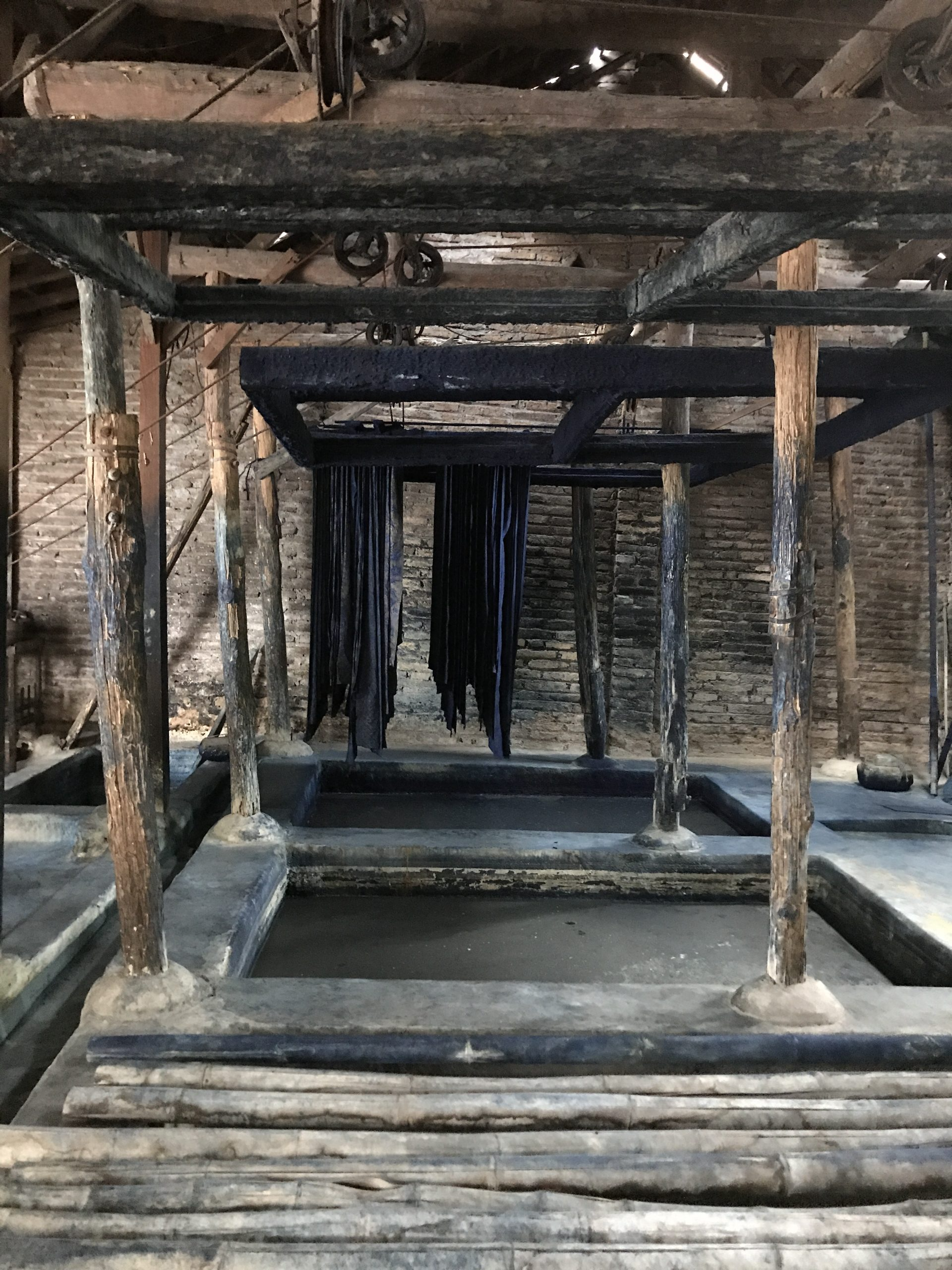
This Traditional Indigo Dye House Has Been Sold And These Indigo Vats Will Be Demolished
The indigo work was one the first dye step in making a traditional natural dye batik. Plant-sourced indigo paste had been used in the past but pre-reduced synthetic indigo replaced the natural indigo material more than twenty years ago, largely without producers knowing the difference. With the market in Jakarta and Bandung being primarily for low-priced cloths that are printed black instead of dyed indigo, we found that indigo dye houses are being closed.
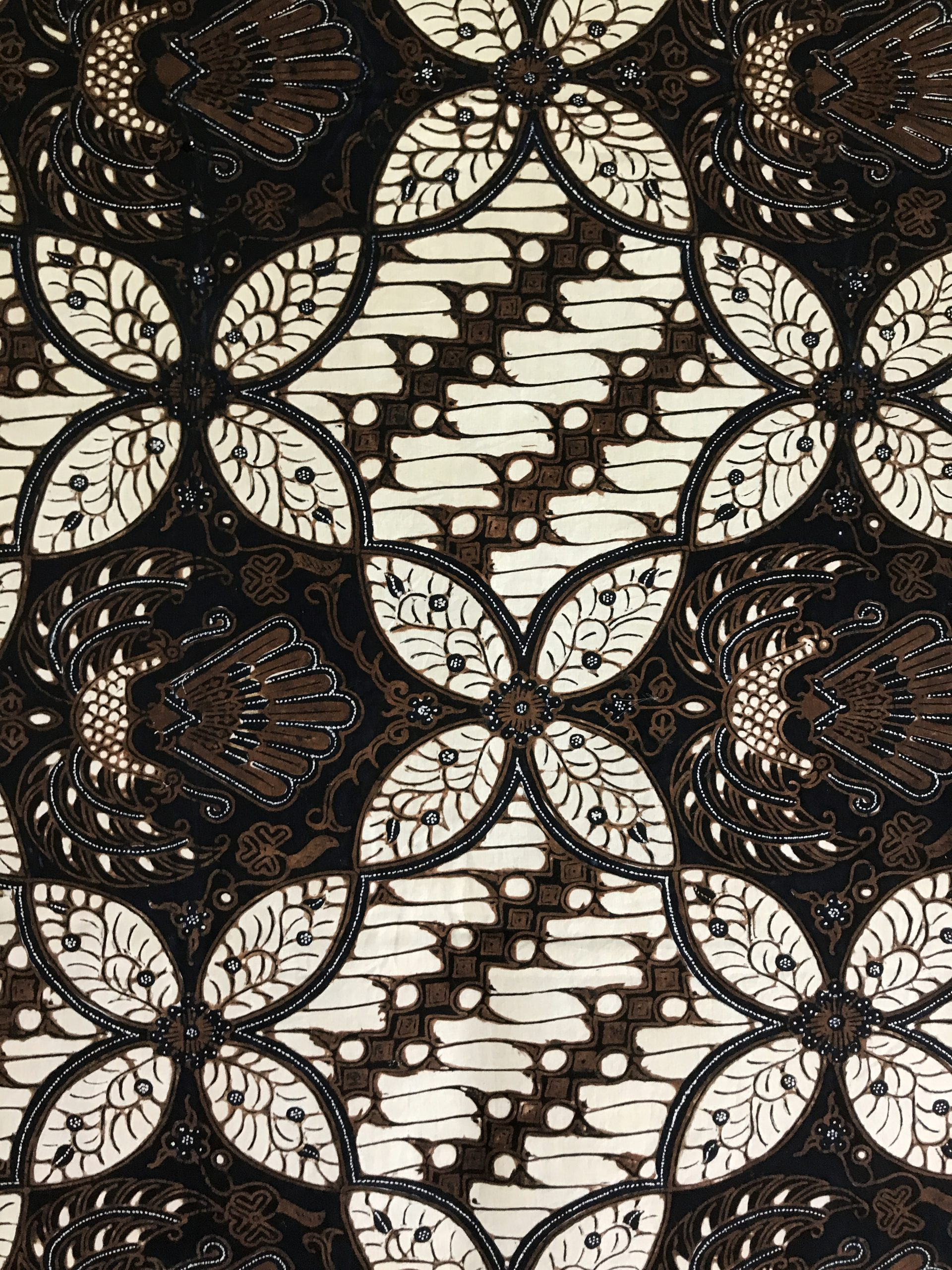
A Textile Of This Quality Would Take More Than 3 Months To Complete Using Multiple Applications Of Wax On Both Sides Of The Textiles And Dyeing With Indigo And Soga
In Yogyakarta we found that high-end traditional batik work is also being threatened due to the economic downturn and loss of a market that supports this work. Making a textile such as this piece, which we purchased from our producer-friend in Yogyakarta, requires years of experience. Different waxes are used for the main design, to outline the white areas, and to fill the areas to be kept white. All waxes are applied by hand using a canting tool. A good textile is waxed equally on the front and back so that it is barely discernably which side is the front.
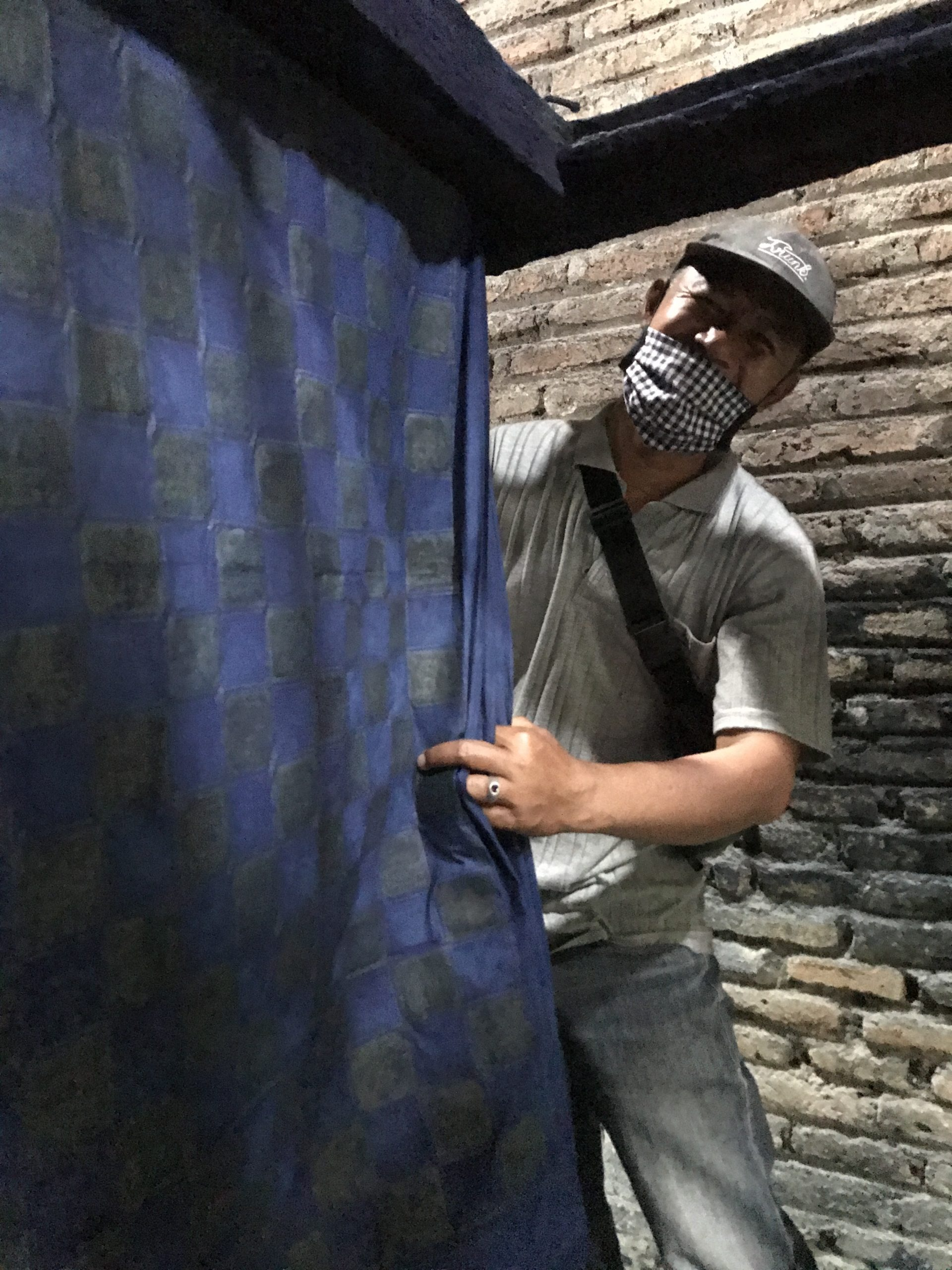
With Pung Working On These Challenges I Have High Hopes That We Will Succeed.
As with arts all over the world at this time, the pandemic is threatening batik’s survival. This is why we will continue to support Brahma Tirta Sari and others who are struggling to survive. Our work with Lou Zeldis batik artisans will require a year or two to transition back into natural indigo dye work and find sustainably sourced dye plants for the soga browns. As always, Pung feels confident that we can make this transition. Before we left, he had Lou’s soga dyer very attentive about how to make an indigo vat from plant-sourced paste so that he can take over the indigo work from the closing indigo studio.